As process measurements are addressed in the production of ethanol, it has become evident that the condensate measurement in the evaporators has become a problem area. With multiple evaporators in parallel and fouling being selective and not universal, indentifying a particular condenser problem has become increasingly critical to the overall plant operation. In practice, this means you must be able to accurately and consistently measure condensate flow on each unit. By doing so, you can monitor individual unit flow rates and as the flow rates start to decrease on particular units, it allows operation and maintenance to identify and single out the problem unit for maintenance while allowing the rest of the plant to remain operational.
The problem is being able to identify a specific condenser problem reliably and accurately through existing measurement technology. Typical technologies, which primarily consist of volumetric flow devices, face many problems due to the application requirements. Initial attempts at volumetric measurements include mechanical or insertion type measurement products, and while less expensive, have shown over time not to be reliable. The problem is that as the condenser begins to foul, the fouling particulate that plugs condenser also effects, shifts, or destroys these measurement technologies. Add in the very low velocities, low conductivity, and relatively high temperatures and it severely limits the options for a reliable and accurate measurement solutions.
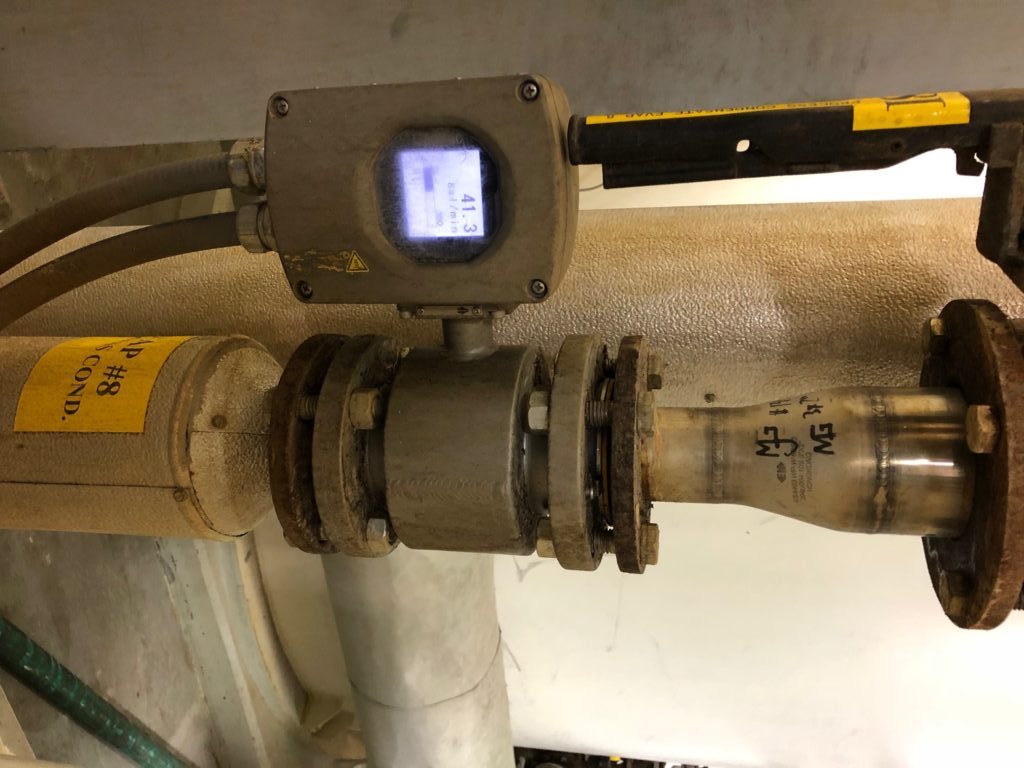
While not designed to address this particular Industry, the CMAG offers an excellent solution to this problem. Designed specifically for condensate applications, it has already addressed all of these application obstacles. Having no moving parts, extreme resistance to fouling, high operational temperature, extremely low operational conductivity, and unmatched low velocity turndown capability, it is becoming the ideal application solution. The CMAG is able to mount in line and in any position (vertical, horizontal, or at an angle) and provides a local display with both analog and digital outputs for integration into plant control systems. With extreme low velocity capability, pipe size reductions are not necessary in order to make accurate, repeatable, and reliable measurements.
Over the last few years the CMAG has made its way into many Ethanol facilities throughout the North America, to date, primarily via “word of mouth” from plant to plant. However, as time has proven the CMAG’s functionality and operational reliability, we would like to formally introduce it as a documented application solution for this industry.
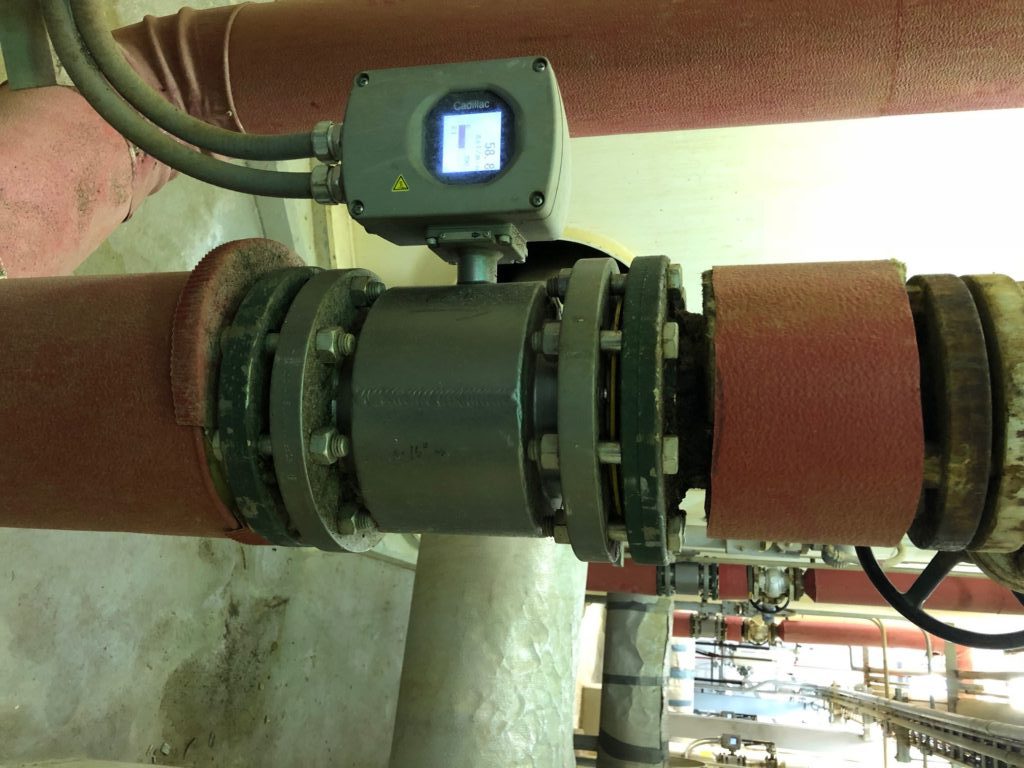